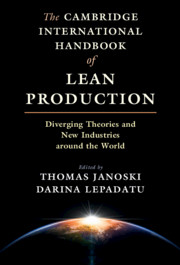
Book contents
- The Cambridge International Handbook of Lean Production
- The Cambridge International Handbook of Lean Production
- Copyright page
- Dedication
- Contents
- Tables
- Figures and Sidebars
- Preface
- Acknowledgments
- Contributors
- Abbreviations
- 1 Lean Production as the Dominant Division of Labor
- Part I Theories of Lean Production
- 2 Lean Production from the View of Management Theory
- 3 Lean Production – Perspectives from its Primary Caretaker, Industrial Engineering
- 4 The Industrial Relations Perspective on Lean Systems, Workers, and Unions
- 5 Contested Views of Lean Production from the Social Sciences Perspective
- 6 The Lean Labor Process
- Part II Lean Production across Industries
- Part III Lean Production Around the World
- Name Index
- Subject Index
- References
3 - Lean Production – Perspectives from its Primary Caretaker, Industrial Engineering
from Part I - Theories of Lean Production
Published online by Cambridge University Press: 11 March 2021
- The Cambridge International Handbook of Lean Production
- The Cambridge International Handbook of Lean Production
- Copyright page
- Dedication
- Contents
- Tables
- Figures and Sidebars
- Preface
- Acknowledgments
- Contributors
- Abbreviations
- 1 Lean Production as the Dominant Division of Labor
- Part I Theories of Lean Production
- 2 Lean Production from the View of Management Theory
- 3 Lean Production – Perspectives from its Primary Caretaker, Industrial Engineering
- 4 The Industrial Relations Perspective on Lean Systems, Workers, and Unions
- 5 Contested Views of Lean Production from the Social Sciences Perspective
- 6 The Lean Labor Process
- Part II Lean Production across Industries
- Part III Lean Production Around the World
- Name Index
- Subject Index
- References
Summary
Because key building blocks of lean production have emerged from concepts native to industrial engineering, it is reasonable to assert that we industrial engineers (IEs) have served as primary caretakers of the lean production/lean management movement. For all that, however, a few concepts once widely admired and practiced by IEs (e.g., process layouts; economic order quantities) have been shown to be at odds with the dictates of lean and its closely linked predecessor, just-in-time production. But IEs adapt, casting off what are found to be dubious and readily adopting such later-arriving essentials of lean as cells and kanban.
- Type
- Chapter
- Information
- The Cambridge International Handbook of Lean ProductionDiverging Theories and New Industries around the World, pp. 64 - 91Publisher: Cambridge University PressPrint publication year: 2021