3 - Steady-State Characteristics of Circuit Components
Published online by Cambridge University Press: 05 June 2012
Summary
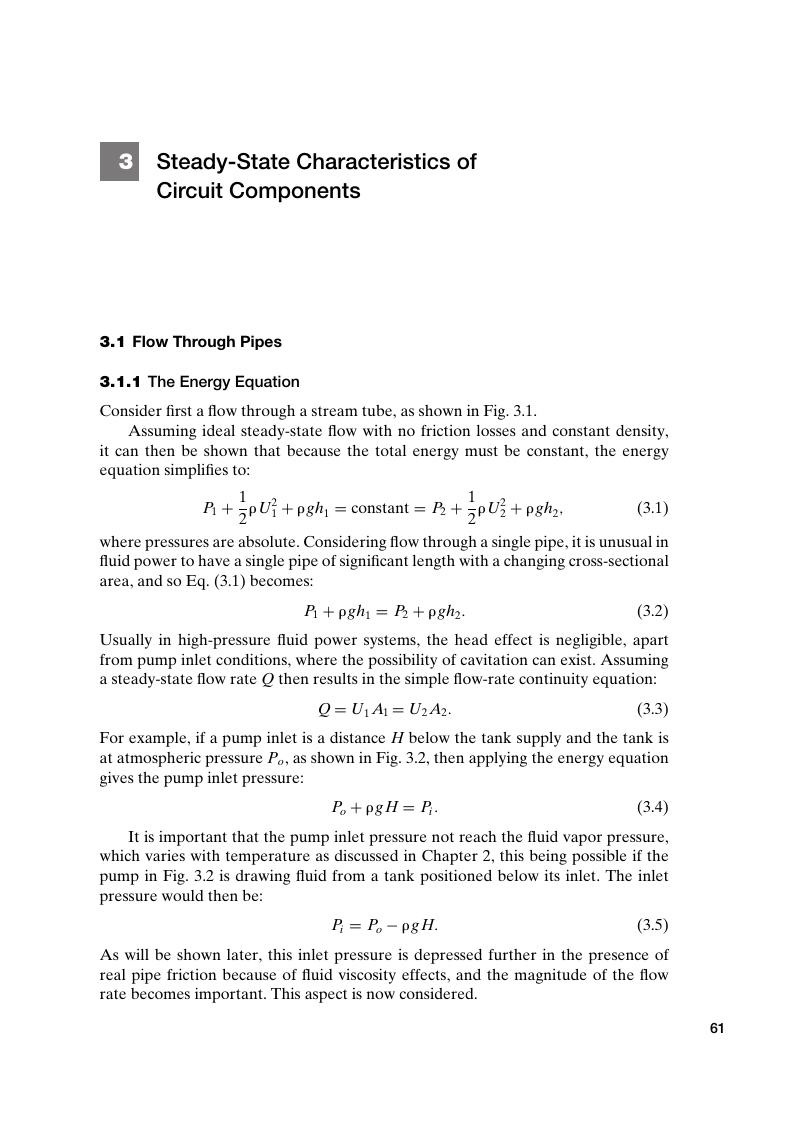
- Type
- Chapter
- Information
- Fundamentals of Fluid Power Control , pp. 61 - 170Publisher: Cambridge University PressPrint publication year: 2009
References
- 1
- Cited by