Introduction
Because it is renewable, widely available and easily transported, biomass energy has attracted wide attention (Gan et al., Reference Gan, Niu, Qu and Zhou2022; Li et al., Reference Li, Wang, Zhou, Dai, Deng, Liu, Cheng, Liu, Cobb, Chen and Ruan2021). Among common conversion technologies, biomass gasification is a prospective technique to produce syngas and other valuable chemicals (Ashok et al., Reference Ashok, Dewangan, Das, Hongmanorom, Wai, Tomishige and Kawi2020; Ren et al., Reference Ren, Yang and Liu2021a). However, tar formation presents a significant challenge for the further development of biomass gasification (Lu et al., Reference Lu, Xiong, Fang, Li, Li and Li2020a). For example, tar condensation can damage downstream equipment, form carbon deposits and increase the cost of biomass gasification. Thus, effective removal of tar is needed before syngas utilization (Ashok & Kawi, Reference Ashok and Kawi2013; He et al., Reference He, Hu, Yin, Xu, Han, Li, Ren, Su, Wang and Xiang2020; Zou et al., Reference Zou, Chen, Zhang, Chen, He, Dang, Ma, Chen, Toloueinia, Zhu, Xie, Liu and Suib2018).
Recently, catalytic reforming has received significant attention for its ability to effectively remove tar during biomass gasification. Many metal-supported catalysts, such as Ni (Ren et al., Reference Ren, Cao, Yang, Liu, Tang and Zhao2021b), Co (Wang et al., Reference Wang, Li, Watanabe, Tamura, Nakagawa and Tomishige2014), Fe (Adnan et al., Reference Adnan, Muraza, Razzak, Hossain and de Lasa2017), Pt (Furusawa et al., Reference Furusawa, Saito, Kori, Miura, Sato and Suzuki2013), and Rh (Mei et al., Reference Mei, Lebarbier, Rousseau, Glezakou, Albrecht, Kovarik, Flake and Dagle2013), have been reported as being effective at removing tar because of their ability to cleave C–C and C–H bonds (Ren et al., Reference Ren, Cao, Zhao, Wei, Zhu and Wei2017). Ni-based catalysts have attracted wide interest because of their catalytic activity and low cost compared to other catalysts (Zhou et al., Reference Zhou, Chen, Gong, Wang, Zhu and Zhou2020). Nevertheless, there are serious problems with Ni sintering in addition to coke deposition during the process. To solve these problems, some transition metals (Fe, Ce, Rh, Co) are usually introduced (Asadullah et al., Reference Asadullah, Miyazawa, Ito, Kunimori, Koyama and Tomishige2004; Kathiraser et al., Reference Kathiraser, Ashok and Kawi2016; Wang et al., Reference Wang, Li, Koike, Watanabe, Xu, Nakagawa and Tomishige2013). Previous studies have indicated that Fe-Ni bimetallic catalysts perform well in catalytic reforming of biomass tars (Zhang et al., Reference Zhang, Zou, Liu, Chen, Dong, Ji, Chen, Xu, Xie, Zhu, Suib and Chen2022; Zou et al., Reference Zou, Chen, Zhang, Chen, He, Dang, Ma, Chen, Toloueinia, Zhu, Xie, Liu and Suib2018). The formation of Fe-Ni alloys can significantly improve the oxygen coverage on the catalyst surface, accelerate the conversion of carbon intermediates and inhibit the generation of carbon accumulation (Wang et al., Reference Wang, Yuan and Ji2011).
Proper support is essential for enhancing the catalytic activities of catalysts (Dong et al., Reference Dong, Chen, Xu, Liu, Wang, Zhang, Ji, Xu, Zhu, Li and Zou2022). A good support for catalytic steam reforming reactions should have a large specific surface area, strong interaction with active metals, and provide acidic or basic centres (Ashok et al., Reference Ashok, Dewangan, Das, Hongmanorom, Wai, Tomishige and Kawi2020). These advantages are conducive to preventing metal sintering and coke deposition during the CSRT process. Recently, the use of natural mineral materials has attracted significant attention for biomass tar conversion because of their superior physicochemical properties, special structures, low cost and wide availability (Chen et al., Reference Chen, Chen, Liu, Zhang, Wang, Dong, Chen, Xie, Zou, Suib and Li2020; Liu et al., Reference Liu, Chen, Chang, Chen, He, Yuan, Xie and Frost2013; Mekki et al., Reference Mekki, Mokhtar, Hachemaoui, Beldjilali, Meliani, Zahmani, Hacini and Boukoussa2021; Xue et al., Reference Xue, Guo, Liu and Chen2018; Zhou et al., Reference Zhou, Shen, Liu and Liu2011). Palygorskite (Pal), an aluminium-magnesium silicate clay mineral, has shown great potential as a catalyst support in the environmental catalysis field (Ezzatahmadi et al., Reference Ezzatahmadi, Millar, Ayoko, Zhu, Zhu, Liang, He and Xi2019; Santanna et al., Reference Santanna, Silva, Silva and Castro Dantas2020). Previous studies have shown that Pal clay-supported Fe-Ni (Fe-Ni/Pal) catalysts displayed distinguished capabilities in toluene reforming. Fe-Ni alloys were well distributed on the surface of Pal and exhibited high reactivity for toluene conversion (Zou et al., Reference Zou, Chen, Zhang, Chen, He, Dang, Ma, Chen, Toloueinia, Zhu, Xie, Liu and Suib2018). However, most of the Pal clays used in the studies above needed a complicated purification process.
In fact, the low-grade Pal clay ore has large reserves around the world but without effective development and utilization. The Pal clay with red color is one of the low-grade Pal clays, which is widely distributed in Linze, Gansu province, China. Previous studies have demonstrated that the reason for the red color of Pal clay should be ascribed to the existence of iron oxides and the substituted iron in the Pal structure (Lu et al., Reference Lu, Zhang, Wang and Wang2022). The proportion of iron oxides and/or the substituted iron in red-colored Pal clay could account for 4–8 wt.% (Lu et al., Reference Lu, Zhang, Wang and Wang2022; Zhang et al., Reference Zhang, Wang, Tian, Wang and Wang2018). This red-colored Pal clay with relatively large Fe content is referred to here as Fe-rich Pal (FePal). Recently, researchers have been attempting to decolorize the FePal to develop its potential uses (Lu et al., Reference Lu, Xiong, Fang, Li, Li and Li2020a; Lu et al., Reference Lu, Zhang, Wang and Wang2022; Zhang et al., Reference Zhang, Wang, Kang, Wang and Wang2018). However, a rare study related to the utilization of raw FePal has been reported (Zhang et al., Reference Zhang, Wang, Kang, Wang and Wang2018). Therefore, a facile and environmentally friendly strategy to use the raw FePal was proposed. FePal was employed as a supporting material to synthesize FePal-supported Ni catalysts (Nix/FePal) for CSRT. The iron oxides and/or the substituted iron in FePal can be used directly as the iron precursor to avoid the addition of chemical ferric salts. And only nickel salts were needed in this catalyst system.
Herein, Nix/FePal catalysts were prepared by using the raw FePal as a support for CSRT. The main aims were: (1) to verify the Nix/FePal catalysts for CSRT; (2) to reveal the interaction between Ni and the Fe in Fe-rich Pal clay; and (3) to explore the possible deactivation reasons for the catalyst during the CSRT process.
Experimental
Catalyst preparation
The raw FePal obtained from Linze, Gansu Province, was crushed and ground into particles of <0.075 mm. According to the XRF measurement, the constituents of raw FePal were SiO2 55.12 wt.%, Al2O3 18.20 wt.%, Fe2O3 7.07 wt.%, MgO 2.91 wt.%, CaO 2.59 wt.%, K2O 3.93 wt.%, and others 2.6 wt.%. The loss on ignition was 7.58 wt.%. Nix/FePal catalysts (x indicates the mass fraction of Ni) with varying Ni loadings (3%, 9%, 14%, 17%) were synthesized via the coprecipitation method. The Fe content of the raw FePal was ~5%, and the mass ratios of Fe/Ni in Nix/FePal catalysts were 5:3, 5:9, 5:14 and 5:17, respectively. After stirring, aging, centrifugation and drying, the acquired samples were ground into small particles (0.85–0.425 mm), the samples obtained were subsequently subjected to calcination in air at various temperatures for 2 h and labelled as Nix/FePal-T (T stands for calcination temperature (CT)). The aforementioned samples were subjected to in-situ reduction in H2 at 700°C for 2 h prior to the CSRT reaction.
Analytical methods
A Shimadzu XRF-1800 instrument (Japan) was used to analyze the chemical composition of the raw FePal material, using Rh radiation. The samples were calcined at 800°C in air to calculate the loss on ignition before the XRF test. X-ray diffraction (XRD) analysis was conducted on both fresh and used catalysts utilizing a Dandong DS-2700 diffractometer. The porous properties of the catalysts were determined using a Nova 3000e analyzer (USA). Temperature-programmed reduction by H2 (H2-TPR) was conducted using an AutoChem Ⅱ 2920 analyzer (USA). Analysis of the formation of carbonaceous species was conducted via Raman spectroscopy using a LabRAM HR Evolution instrument (France). The coke content was assessed utilizing a thermogravimetric analyzer (TG, Germany). Scanning electron microscopy (SEM) was performed using an Hitachi SU8020 (Japan). Transmission electron microscopy (TEM) was conducted using a JEM-1400 flash microscope (Japan).
Experimental system
The CSRT reaction system is illustrated in Fig. 1. To begin the experiment, 0.3 g of catalyst was added to a quartz tube and reduced in a hydrogen atmosphere at a temperature of 700°C for 2 h. The residual H2 was removed with Ar. After that, the desired reaction temperature (500–800°C) was set on the furnace and kept stable until the end of the CSRT experiments. Toluene (3000 ppm) and water (0–42000 ppm) were injected into the pipeline using syringe pumps and mixed thoroughly in a gas mixing tank. The heating tape set to a temperature of 60°C was employed to keep the gas mixture in a gaseous state throughout the reaction. The mixed gases were introduced into the quartz tube to trigger the reactions after the initial concentration of toluene was stable. During the reaction process, the GHSV (gas hourly space velocity) was maintained at a constant value of 17,052 h–1. The composition of the gaseous products was determined by a gas chromatograph (9790II). Toluene conversion, gas yields, gaseous product distributions and the molar ratios of H2/CO were computed based on Eqs S1–S6 (given in the Supplementary Information, SI).

Figure 1. The CSRT reaction system.
Results
Analysis of the catalysts
The XRD patterns of Ni14/FePal calcined in air at various temperatures are shown in Fig. S1. The peaks at 20.9, 26.7, 50.2, 60.0 and 68.0°2θ were attributed to quartz and the peak at 27.9°2θ was attributed to feldspar. According to previous studies, quartz is generally considered to be an inert material and has no almost influence on catalytic performance (Zou et al., Reference Zou, Chen, Liu, Zhang, Ma, Xie and Chen2017). The peaks at 8.6 and 34.9°2θ were attributed to palygorskite in raw FePal (Wang et al., Reference Wang, Gainey, Wang, Mackinnon and Xi2022), while these reflection peaks almost disappeared after calcination at high temperature, indicating that the structure of Pal was destroyed (Chen et al., Reference Chen, Zhao, Zhong and Jin2011). Although a certain amount of iron existed in FePal, no independent phases of iron oxides were observed. This indicated that the iron oxides in FePal were dispersive or below the XRD detection limit. It was worth noting that awaruite (Fe-Ni alloy) was observed at 44.2°2θ (111) and 51.6°2θ (200) in reduced catalysts (Fig. 2a and Fig. 2b), which indicated that Ni interacted strongly with Fe in FePal. In addition, the reflection peaks of awaruite became narrower as the CT and Ni content increased, which indicated the enhancement in crystallinity of awaruite.

Figure 2. XRD patterns of catalysts. Ni14/FePal heat treated in air at various temperatures (a) and Nix/FePal heat treated in air at 600°C (b), and subsequently reduced in H2 at 700°C.
SEM and TEM images of the raw FePal and freshly reduced Nix/FePal catalysts are shown in Fig. 3. Fe, Mg, Al and Si were very dispersed in FePal as shown in the mapping images (Fig. 3a). The characteristic rod-like morphology of Pal is shown Fig. 3b. Even though Pal reflections disappeared after calcination at high temperatures, the original morphology of Pal still could be observed in Fig. 3c. This is as observed in previous studies also (Boudriche et al., Reference Boudriche, Calvet, Hamdi and Balard2012; Wang et al., Reference Wang, Wang, Zhang, Zhang and Liang2020). Many small particles which were well dispersed on the Ni3/FePal and Ni14/FePal surfaces could be observed in Fig. 3d and Fig. 3e, respectively. These small particles could be assigned to Fe-Ni alloys according to XRD (Fig. 2b) and the mapping results. Furthermore, the Fe-Ni alloy particle sizes on Ni3/FePal (Fig. 3f) and Ni14/FePal (Fig. 3g) varied between 5 and 25 nm and the average sizes were 12.6 nm and 13.2 nm, respectively.
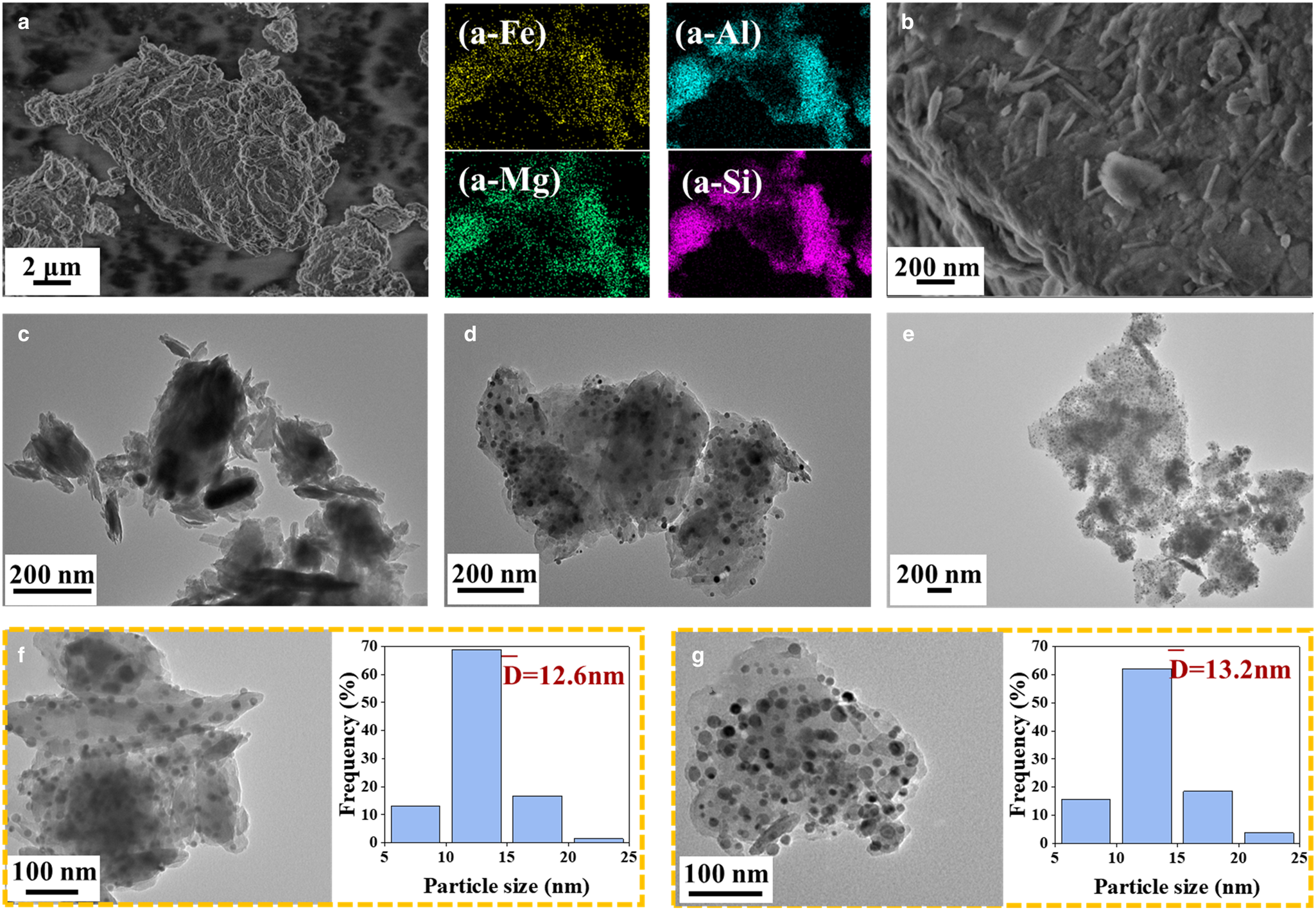
Figure 3. SEM and TEM images of the raw and freshly reduced catalysts: (a,b) raw FePal; (c) freshly reduced FePal; (d,f) freshly reduced Ni3/FePal and the PS distribution of Fe-Ni alloy; (e,g) freshly reduced Ni14/FePal and the PS distribution of the Fe-Ni alloy.
The H2-TPR profiles of FePal and Ni14/FePal are shown in Fig. 4. Five major peaks were observed (228, 302, 382, 572 and 818°C) in the raw FePal. Combined with data from the XRF results, we can see that the FePal contained 7.07% iron oxides. Therefore, these reduction peaks were considered to be the reduction of Fe on the surface and/or in the crystal structure of FePal (Liu et al., Reference Liu, Chen, Chang, Chen, He and Frost2012; Liu et al., Reference Liu, Chen, Chang, Chen, He, Yuan, Xie and Frost2013). Regarding Ni14/FePal, the peak observed at 224°C was due to the reduction of the un-interacted NiO to Ni (Peng et al., Reference Peng, Chen, Zhang, Li, Cui, Guo, Zhao and Zhang2021). The peak observed at 418°C was associated with the reduction of Fe3+ to Fe2+ (Peng et al., Reference Peng, Chen, Zhang, Li, Cui, Guo, Zhao and Zhang2021; Tang et al., Reference Tang, Li, Shen and Wang2013; Zhang et al., Reference Zhang, Hu, Xiang, Xu, Shen, Liu, Xia, Ge, Wang and Li2022). Moreover, the reduction of the strongly interacted NiO with support could be observed at 525°C (Zhang et al., Reference Zhang, Hu, Xiang, Xu, Shen, Liu, Xia, Ge, Wang and Li2022). When Ni was introduced into the system (Ni14/FePal), the reduction peak of Fe2+ to Fe0 was observed to shift from 572°C to 640°C. Meanwhile, the reduction peak of Fe3+ to Fe2+ was observed to shift towards a higher-temperature region, which was attributed to the strong interaction between Fe and Ni (Jiang et al., Reference Jiang, Dou, Wang, Zhang, Song, Chen and Xu2016). The reduction peak at the higher temperatures of FePal (818°C) and Ni14/FePal (780°C) could be interpreted as the reduction of Fe in the crystal structure of Pal (Zhang et al., Reference Zhang, Hu, Xiang, Xu, Shen, Liu, Xia, Ge, Wang and Li2022; Zou et al., Reference Zou, Chen, Liu, Zhang, Ma, Xie and Chen2017). In addition, the ratio of hydrogen consumption between FePal and Ni14/FePal was ~0.24, indicating that the intense reduction reaction occurred over Ni14/FePal. By taking into account the XRD analysis in Fig. 2, Fe and Ni were reduced gradually and subsequently formed Fe-Ni alloys with the increase in reduction temperature.

Figure 4. H2-TPR profiles of FePal and Ni14/FePal.
Effect of Ni content
The catalysts with various Ni contents on CSRT and Eqs S7–S13 represent the possible reactions in CSRT (Fig. 5). The results showed a clear enhancement in both toluene conversion and catalyst stability with the introduction of Ni. The toluene conversions of Nix/FePal were maintained at >97% when the Ni content was >9%. This result could be attributed to the excellent performance of Ni in cleaving C–H and C–C bonds, leading to the formation of smaller and more reactive intermediates that can be further converted to lighter gaseous products. In addition, previous studies have demonstrated that Fe-Ni alloy can enhance the catalytic cracking of hydrocarbon, promoting catalyst reactivity and stability (Zhang et al., Reference Zhang, Hu, Xiang, Xu, Shen, Liu, Xia, Ge, Wang and Li2022; Zou et al., Reference Zou, Chen, Zhang, Chen, He, Dang, Ma, Chen, Toloueinia, Zhu, Xie, Liu and Suib2018).

Figure 5. Effect of Ni content on CSRT: (a) toluene conversion; (b–f) gas yields (reaction conditions: CT = 600°C, RT = 700°C, W = 0.3 g, S/C = 1, GHSV = 17052 h–1).
Based on the gaseous products, the reactions described in Eqs S7–S13 might occur simultaneously during the CSRT. The H2 yield of Ni9/FePal, Ni14/FePal and Ni17/FePal remained stable at >67%. Note that Ni14/FePal exhibited the greatest CO yield (>65%) among Nix/FePal catalysts, indicating the strong Boudouard reaction (Eq. S11) during CSRT over Ni14/FePal. These results indicated that appropriate Ni content was important for CSRT. Insufficient Ni content provided fewer active sites for CSRT, while excessive Ni content would reduce the amount of Fe on the catalysts, leading to the accumulation of coke and decreasing the catalytic efficiency.
Effect of calcination temperature
The catalytic activity of Ni14/FePal for CSRT at various different calcination temperatures is shown in Fig. 6. The toluene conversion exhibited an increasing trend (raw–700°C) and subsequently decreased with further increase in CT (700–800°C). The smaller amount of toluene conversion at low CT was probably because of the low dispersion of active sites, which was not conducive to CSRT (Barzegari et al., Reference Barzegari, Kazemeini, Rezaei, Farhadi and Keshavarz2022). The reduction in toluene conversion at a high CT of 800°C was probably due to the severe sintering of Fe-Ni alloys. The toluene conversion underwent no significant change and was maintained stably at >98% at 600°C and 700°C during the reaction process. There was almost no difference in H2 yields (>66%) at 600°C and 700°C; however, the CO yield reached >67% at 600°C while it was only ~30% at 700°C. Therefore, Ni14/FePal calcined in air at 600°C could maintain the best performance for CSRT.

Figure 6. Effect of calcination temperature of Ni14/FePal on CSRT: (a) toluene conversion; (b–f) gas yields (reaction conditions: RT = 700°C, W = 0.3 g, S/C = 1.0, GHSV = 17052 h–1).
Effect of reaction temperature
The catalytic efficacy of catalysts for CSRT may be influenced significantly by the reaction temperature (RT) (Liu et al., Reference Liu, Chen, Cao, zhang, Mao, Wang, Wang and Kawi2020; Tang et al., Reference Tang, Cao, Yang, Feng, Ren, Wang, Zhao, Zhao, Cui and Wei2020). The effect of RT (500–800°C) on CSRT over Ni14/FePal is illustrated in Fig. 7. With an increase in RT (500–700°C), the toluene conversion improved continuously and reached >98% at 700°C. However, no significant increase in toluene conversion was noted by further increase of the temperature (800°C), indicating that the reactions had approached thermodynamic equilibrium (Zhang et al., Reference Zhang, Hu, Xiang, Xu, Shen, Liu, Xia, Ge, Wang and Li2022). In addition, the catalytic activity was more stable at higher temperatures >700°C, which indicated that the RT had influence over the activity as had the stability of Ni14/FePal. Because of the endothermic character of CSRT (Park et al., Reference Park, Lee, Kwon, Lee, Kang, Hong and Kim2019), hydrocarbons can be decomposed and the carbon intermediates are prone to be oxidized more easily at higher temperatures (Kong et al., Reference Kong, Yang, Fei and Zheng2012).

Figure 7. Effect of reaction temperature of Ni14/FePal on CSRT: (a) toluene conversion; (b–f) gas yields (reaction conditions: W = 0.3 g, S/C = 1.0, GHSV = 17052 h–1).
The H2 yield was stable at ~65% (600–800°C), while the CO yield reached a maximum of 68% at 700°C and declined slightly at 800°C. Similarly, the CO2 yield increased from 6.9% to 8.1% (500–550°C) and then decreased from 8.1% to 0.8% (550–800°C). This phenomenon indicated that Eq. S13 was facilitated at 500–550°C and that the Boudouard reaction (Eq. S11) and water gas reaction (WGR; Eq. S12) were facilitated at 550–800°C. The benzene yield decreased with increasing RT, indicating that the hydrodealkylation reaction (Eq. S9) weakened constantly. According to the results in Fig. S2, the distributions of H2 and CO, and the molar ratio of H2/CO stabilized at ~60% and ~39% and at 1.5 at 700°C, respectively. The syngas with a constant gas component could be used to synthesize some chemicals through Fischer-Tropsch synthesis (Son et al., Reference Son, Lee, Soon, Roh and Lee2013). Therefore, 700°C was the optimum RT for CSRT in this experimental condition.
Effect of S/C ratio
The impact of various S/C ratios on catalytic activity of Ni14/FePal for CSRT at 700°C is shown in Fig. 8. The inclusion of steam greatly enhanced the catalytic activity of Ni14/FePal. Without steam, the toluene conversion and H2 yield exhibited a decrease, dropping from 16% and 4.6% to 2% and 1.8% (S/C = 0.0), respectively; only a little benzene was detected and almost no CO and CO2 were found in gaseous products, indicating that only a toluene-cracking reaction and the deactivation of Ni14/FePal had occurred under this reaction condition. As a result, carbon was deposited on the catalyst surface at a faster rate, causing the catalyst to deactivate quickly. The toluene conversion was observed to increase from 66.6 to 98.3% (0.5–1.0). In particular, when S/C = 1.0, the production of H2 and CO peaked, with yields exceeding 66% and 68%, respectively. This suggested that Eq. S7, Eq. S10 and Eq. S12 dominated during the reaction process, improving the production of H2 and CO. Nevertheless, continuing to improve the S/C molar rate (1.5 and 2.0) seemed to deliver no improvement in toluene conversion, while the H2 and CO yields decreased significantly from 66.2% and 68.7% to 45.6% and 53.6%, respectively. In addition, the yield of CO2 increased from 0.8% to 9.8%. This suggested that the reactions of Eq. S8 and Eq. S13 were likely to be enhanced. As displayed in Fig. S3, with S/C molar ratio increased, the H2 distribution remained stable at 64%, whereas the CO distribution decreased from 37 to 30%. At the same time, the CO2 distribution increased from 0 to 5%. These fluctuations caused an increase in the H2/CO molar ratio (1.7 to 2.2). The presence of steam could lead to adsorption saturation, which negatively affected catalyst activity (Gao et al., Reference Gao, Wang, Li, Wu and Yin2016). Excessive steam could also absorb a significant amount of heat and reduce the RT (Liu et al., Reference Liu, Chen, Cao, zhang, Mao, Wang, Wang and Kawi2020), leading to energy consumption and reduced catalytic activity. Therefore, S/C = 1.0 was the best for CSRT under the current conditions.

Figure 8. Effect of S/C ratio of Ni14/FePal on CSRT: (a) toluene conversion; (b–f) gas yields (reaction conditions: RT = 700°C, W = 0.3 g).
Lifetime evaluation
To evaluate the stability of Ni14/FePal, the reforming reaction was carried out for 62 h. As shown in Fig. 9, Ni14/FePal exhibited outstanding stability in toluene conversion and gas yields. The toluene conversion, H2 and CO yields were approximately maintained at 98%, 63% and 64%, respectively. In addition, the CO2, CH4 and benzene amounts were negligible (Fig. 9a). In accordance with the toluene conversion and gas yields obtained in the experiment, the carbon conversion of Ni14/FePal was estimated to be ~68.3%. The H2/CO molar ratio fluctuated between 1.5 and 1.6 (Fig. 9b). The highly dispersed Fe-Ni alloys could promote the activation of toluene molecules, which effectively prevented the carbon deposition and metal sintering, maintaining the activity of the catalyst (Zhang et al., Reference Zhang, Cheng, Lu, Ding and Zhou2009). The comparison with other catalysts for toluene conversion in Table S1 further indicated the excellent catalytic activity of Ni14/FePal. Therefore, Ni14/FePal was good for CSRT and syngas production.

Figure 9. Lifetime evaluation of Ni14/FePal for CSRT: (a) toluene conversion and gas yields; (b) H2/CO molar ratio (reaction conditions: RT = 700°C, W = 0.3 g, S/C = 1.0).
Kinetics study
The kinetics constants can be calculated using kinetics models. In this study, the reaction could be considered a quasi-first-order kinetics model (Mani et al., Reference Mani, Kastner and Juneja2013). In order to obtain dependable kinetics parameters of the Ni14/FePal catalyst for CSRT, the toluene conversion should be controlled at <25% (Oemar et al., Reference Oemar, Ming Li, Hidajat and Kawi2014; Xie et al., Reference Xie, Shu, Chen, Liu, Zou, Wang, Han and Chen2022). In addition, kinetics research should be performed without heat- or mass-transfer resistance. The reaction conditions for the kinetics study are presented in the supplementary information (SI). The toluene conversion increased first and then fluctuated slightly, indicating that external mass-transfer resistance had almost no effect on the reaction at gas-flow rates exceeding 200 mL/min (Fig. S4). The kinetics model can be expressed with Eqs S14–S17.
Based on the results in Fig. 10, the apparent activation energy (E a) and pre-exponential factor (A) of Ni14/FePal were calculated and reported in Table 1. The outcomes of the comparison indicated that the Ni14/FePal had a smaller E a value (33.99 kJ mol−1) than the other catalysts, demonstrating that the Ni14/FePal catalyst had high reactivity for CSRT.

Figure 10. The effect of RT on the toluene conversion of Ni14/FePal (a), and the Arrhenius plot for the calculation of E a (b). Reaction conditions: W = 3 mg, flow rate = 200 mL/min, GHSV = 3.4×106 h-1, S/C = 1.0, t = 30 min.
Table 1. Kinetics parameters for CSRT over Ni14/FePal catalyst and comparison with previous studies in the field.

ng = not given.
Characterization of the catalysts used
BET and XRD
The specific surface area (SSA), total pore volume (TPV), and crystal size (CZ) values of the catalysts before and after the CSRT reaction are listed in Table 2. With an increase in RT (500 to 800°C), the SSA and TPV of Ni14/FePal decreased from 85.7 m2/g and 0.26 cm3/g to 22.1 m2/g and 0.09 cm3/g, respectively. Conversely, the CZ increased from 10.2 nm to 24.7 nm. There was a decrease in SSA and an increase in the CZ of Nix/FePal compared to equivalent values before the reaction. These results could be attributed to the formation of carbon deposits and the sintering of active components at higher temperatures.
Table 2. Physicochemical properties of the catalysts.

nd = not detectable.
a The Debye-Scherrer equation can be conveniently applied to calculate particle sizes of <60 nm.
b Nix/FePal catalysts calcined in air at 600°C followed by H2 reduction at 700°C.
c Ni14/FePal-RT-S/C.
As shown in Fig. 11, Fe-Ni alloy peaks could be still observed at 44.2°2θ (111) and 51.6°2θ (200) in all catalysts after the reaction. The Fe-Ni alloy peaks became narrower (Fig. 11a) compared to that of the raw catalyst before the reaction (Fig. 2b). Similarly, the peaks of Fe-Ni alloys over Ni14/FePal reacted under various temperatures became stronger and narrower as the temperature increased (Fig. 11b), indicating that the CZ became larger after reaction, which was in agreement with the variation of CZ in Table 2. The peaks of the Fe-Ni alloys were narrowest, compared to the other catalysts, after calcination at 800°C (Fig. 11c), suggesting that the Fe-Ni alloy was more prone to sintering at high temperatures. Fe-Ni alloy peaks changed slightly as the S/C ratio increased (Fig. 11d), in agreement with CZ values in Table 2 which were calculated using the Scherrer equation.

Fig. 11. XRD patterns of the used catalysts: (a) reacted at 700°C; (b) Ni14/FePal reacted at various temperatures; (c) Ni14/FePal calcined at various temperatures; (d) Ni14/FePal reacted at various S/C molar ratios.
SEM and TEM analysis
SEM and TEM images, EDS mapping and the particle-size (PS) distributions of Fe-Ni alloys of the used catalysts are shown in Fig. 12. The morphology of the FePal support remained rod-like even after the reaction (Fig. 12a,b). Many highly dispersed small particles were observed in the SEM and TEM images. According to the XRD and EDS mapping results, these small particles were assigned to Fe-Ni alloys. As displayed in Fig. 12c,d, Ni3/FePal and Ni14/FePal reacted at 700°C showed minimal filamentous carbon deposition. This could be attributed to the high RT preventing the formation of filamentous coke, thus facilitating the decomposition of toluene to CO or CO2, improving the conversion of carbon. Nevertheless, filamentous carbon accumulation could be clearly observed in Ni14/FePal reacted at 500°C in Fig. 12e, which could be attributed to the accumulation of graphite-type coke (Yao et al., Reference Yao, Zhang, Williams, Yang and Chen2018). This form of coke deposition would blanket the catalyst surface, inhibiting the catalytic activity of the active species (Choong et al., Reference Choong, Zhong, Huang, Wang, Ang, Borgna, Lin, Hong and Chen2011). The particle sizes of Fe-Ni alloys were between 5 and 40 nm; the average sizes of the Ni3/FePal-700, Ni14/FePal-700 and Ni14/FePal-500 were 27.1 nm, 14.9 nm and 17.1 nm, respectively. This indicated that the sintering phenomenon occurred in the reforming reactions. However, according to the results in Fig. 7, this degree of sintering had no significant impact on the catalytic activity of Ni14/FePal.

Figure 12. SEM images and EDS mapping, TEM images and the particle-size distributions of the Fe-Ni alloy of the used catalysts. (a,c) Ni3/FePal-700; (b,d) Ni14/FePal-700; (e) Ni14/FePal-500.
Coke-deposition analysis
Raman spectroscopy is a useful tool for analyzing the structure and level of graphitization of the coke deposits (Yao et al., Reference Yao, Wu, Yang, Zhang, Nahil, Chen, Williams and Chen2017). The D-band and G-band (~1350 and ~1590 cm−1, respectively) represent the amorphous and ordered graphite carbon, respectively (Gong et al., Reference Gong, Liu, Wan, Chen, Wen, Mijowska, Jiang, Wang and Tang2012; He et al., Reference He, Liu, Meng, Sun, Biswas, Shen, Luo, Miao, Zhang, Mustain and Suib2016). The D/G ratio intensity is a significant indicator for estimating the graphitization or the disorder of carbon deposition (Lu et al., Reference Lu, Xiong, Fang, Li, Li and Li2020b; Son et al., Reference Son, Lee, Song, Jeon, Jung, Yun, Jeong, Shim, Jang and Roh2014). For example, a higher D/G ratio indicates that more amorphous carbon formed in the carbon structure. As the Ni content increased from 0 to 9% (Fig. 13a), the D/G ratio of the used catalysts increased, indicating that less graphite-type carbon had accumulated. In contrast, the intensities of Raman bands of Nix/FePal decreased continuously as the Ni content increased, suggesting a reduction in coke accumulation. This phenomenon suggested that a greater Ni content in the catalyst facilitated the formation of more Fe-Ni alloys, which in turn inhibited carbon accumulation (Chen et al., Reference Chen, Chen, Liu, Zhang, Wang, Dong, Chen, Xie, Zou, Suib and Li2020). The D/G ratio kept decreasing as the RT increased in Fig. 13b, suggesting that the graphite carbon tented to form under high temperatures. The higher D/G ratio suggested a greater disorder of carbon deposition and a lower impact on catalytic activity (García-Diéguez et al., Reference García-Diéguez, Pieta, Herrera, Larrubia and Alemany2010; Quek et al., Reference Quek, Liu, Cheo, Wang, Chen and Yang2010). The intensities of Raman bands of Ni14/FePal became lower as the RT exceeded 650°C, demonstrating that a smaller amount of coke deposition had occurred. Combined with the results in Fig. 7, one possible explanation was that the catalytic activity of Ni14/FePal was primarily associated with the amount of coke deposition rather than the types (Zou et al., Reference Zou, Chen, Zhang, Chen, He, Dang, Ma, Chen, Toloueinia, Zhu, Xie, Liu and Suib2018). The D/G ratio increased gradually and then stayed at 0.94, while the intensities of Raman bands reduced with increasing S/C molar ratio (Fig. 13c). This demonstrated that the formation of graphite-type coke was effectively controlled after the addition of steam.

Figure 13. Raman spectra of the spent catalysts: (a) Nix/FePal; (b) effect of RT on Ni14/FePal; (c) effect of S/C molar ratio on Ni14/FePal.
TG analysis was utilized to quantify the amount of coke deposited on the spent Ni14/FePal. The curves indicated that four stages of weight variations had occurred during oxidation of the used catalyst (Fig. 14a): (1) the weight loss at <100°C was due to the desorption of surface-adsorbed water molecules from the catalyst surface; (2) the weight loss at 100–250°C was considered to be a result of the elimination of amorphous carbon; (3) the weight increase at 250–500°C could be explained by the oxidation of Ni and Fe; and (4) the weight loss at 500–650°C was due to the elimination of graphite coke (Gao et al., Reference Gao, Han and Quan2018; Gao et al., Reference Gao, Chen, Lai and Quan2021). The amount and accumulation rate of coke deposition (calculated using Eq. S18) was shown in Fig. 14b to decrease with RT increasing from 500 to 800°C. The amount and accumulation rate of coke deposition were 0.12% and 0.6 mgC/gcath at 700°C, respectively. Moreover, the production of graphite coke was scarcely visible at 800°C. This indicated that the accumulation of coke could be effectively inhibited at high reaction temperatures.

Figure 14. TG curves (a) and the amount of coke deposition of the used Ni14/FePal catalyst (b) at various reaction temperatures.
Conclusions
In this study, the red Fe-rich palygorskite clay (FePal) was utilized as the support to prepare the Nix/FePal catalysts for CSRT. The iron in FePal could react with Ni during the reduction process to form the Fe-Ni alloys (awaruite) which were proven to be the active components for toluene conversion. Calcination under air atmosphere at an appropriate temperature could facilitate the dispersion of active components. Ni14/FePal had the greatest catalytic activity among Nix/FePal catalysts for CSRT. Under optimal reaction conditions (CT = 600°C, RT = 700°C, and S/C = 1.0), >98%, >66% and >68% toluene conversion, H2 and CO yields, respectively, were obtained over Ni14/FePal. The kinetics study indicated that the E a of Ni14/FePal was 33.99 kJ mol−1, which further confirmed the superior catalytic activity of Ni14/FePal for toluene conversion. Moreover, the high dispersion of Fe-Ni alloys and excellent coke resistance enabled Ni14/FePal to maintain high stability and reactivity for toluene conversion. This strategy using the FePal as a support for CSRT provided an alternative catalyst for tar conversion and might also promote its application in heterogeneous catalysis.
Financial support
This study was supported financially by the National Natural Science Foundation of China (No. 41872040), Anhui Provincial Natural Science Foundation (No. 2108085QD164), and the fundamental Research Funds for the Central Universities (No. JZ2020HGTA0088).
Supplementary material
The supplementary material for this article can be found at https://doi.org/10.1180/clm.2023.12.