Introduction
Naphtha is a fraction of petroleum which typically makes up 15–30 wt.% of crude oil and boils at between 30 and 200°C; this naptha mixture consists of hydrocarbon molecules with 5–10 carbon atoms. The light naphtha (C5 and C6) is suitable for thermal cracking, while the medium naphtha (C7–C9) is the preferred feed for catalytic reforming (Rodríguez & Ancheyta Reference Rodríguez and Ancheyta2011). Consequently, a huge potential market exists for naphtha (Kulprathipanja Reference Kulprathipanja1991). The separation of n-paraffins and branched paraffins from naphtha is vital in the petroleum and petrochemical industries because n-paraffins are very important chemical raw materials of alkylbenzene, benzenesulfonate synthetic detergent, lubricant additives, paraffin oil, and so on (Liu et al. Reference Liu, Shen and Sun2006). Adsorption processes based on shape-selective 5A sieves were effective and economical at separating n-paraffins from naphtha and improved the utilization efficiency of naphtha (Silva et al. Reference Silva, Da Silva and Rodrigues2000).
n-Hexane is a light liquid paraffin, which can produce high-quality solvent oils and ethylene (Liu et al. Reference Liu, Shen and Sun2006). The major applications are the so-called MaxEneTM process from Universal Oil Products Company (UOP) (Holcombe Reference Holcombe1979, Reference Holcombe1980; Mendes et al. Reference Mendes, Rodrigues, Horcajada, Serre and Silva2014) with the full-range naphtha, C4–C10, as the raw material, using liquid-phase, simulated moving-bed technology (Flank et al. Reference Flank, Fethke and Marte1989; Sun et al. Reference Sun, Shen and Liu2008). Foley et al. (Reference Foley, Greer and Pujado2001) studied the MaxEneTM process and determined that the n-alkanes made up ~85–87% of the desorbed oil. However, this method is expensive and requires complex equipment.
Molecular sieves are crystalline aluminosilicates. 4A and 5A molecular sieves are both artificial zeolites of Linde Type A (LTA) topology in sodium and sodium/calcium forms, which possess cavities with uniform size and shape. The cavities are present in the rigid, three-dimensional networks with silica and alumina tetrahedra that link together through oxygen bridges (Zhang et al. Reference Yuan, Yin, Liu, Li and Sun2012; Bandura et al. Reference Bandura, Franus, Józefaciuk and Franus2015). 5A zeolite possesses pores suitable for sieving (0.51 nm) to accommodate linear and to exclude branched paraffins (Chen et al. Reference Chen, Wang, He, Chen and Zhang2016). The separation of linear from branched alkanes using 5A zeolite was a major success even in the petrochemical industry of today (Peralta et al. Reference Peralta, Chaplais, Simon-Masseron, Barthelet and Pirngruber2012). 5A zeolites are used widely as adsorbents for selectively separating n-alkanes from naphtha or petroleum feedstocks (Sun et al. Reference Sun, Liu, Huang and Shen2006; Loughlin & Abouelnasr Reference Loughlin and Abouelnasr2012; Cao et al. Reference Cao, Liu, Shen and Sun2013; Herm et al. Reference Herm, Wiers, Mason, van Baten, Hudson, Zajdel, Brown, Masciocchi, Krishna and Long2013).
Natural clay minerals have been used widely in the synthesis of zeolites, due to their low cost, environmentally friendly applications, and being an environmentally benign Si/Al source (Villaquirán-Caicedo et al. Reference Villaquirán-Caicedo, de Gutiérrez, Gordillo and Gallego2016; Yuan et al. Reference Yuan, Yin, Liu, Li and Sun2016; Novembre & Gimeno Reference Novembre and Gimeno2017; Xie et al. Reference Xie, Qian, Qi, Wu, Liu and Sun2018). To prepare 5A zeolite (Ca-zeolite), 4A zeolite (Na-zeolite) could be exchanged by calcium cations using dilute solutions of calcium chloride at moderate temperatures. Synthesis, properties, characterization, and applications of zeolite A have been well documented (Li et al. Reference Li, Beachner, McManama and Hanlie2007; Montanari et al. Reference Montanari, Salla and Busca2008; Mohamed et al. Reference Mohamed, Ismail, Kini, Ibrahim and Koopman2009; Taffarel & Rubio Reference Taffarel and Rubio2010; Li et al. Reference Li, Jean, Jiang, Chang, Chen and Liao2011). In those studies, 4A zeolite was usually prepared from kaolin and 5A zeolite was obtained through ion exchange of 4A zeolite (Shams & Mirmohammadi Reference Shams and Mirmohammadi2007; San Cristóbal et al. Reference San Cristóbal, Castelló, Martín Luengo and Vizcayno2010; Melo et al. Reference Melo, Riella, Kuhnen, Angioletto, Melo, Bernardin, da Rocha and da Silva2012), while zeolite A has occasionally been synthesized from natural palygorskite (PAL) (Li et al. Reference Li, Jiang, Liu, Shi, Zhang and Sun2017).
The synthesis and characterization of 5A zeolite using PAL and sodium aluminate precursors was reported by Chen et al. (Reference Chen, Wang, He, Chen and Zhang2016). PAL is a well defined Si/Al-containing clay mineral, which is abundant and cheap in China (Shao et al. Reference Shao, Chen, Zhong, Leng and Wang2015). It offers silica (SiO2) and alumina (Al2O3) for the synthetic manufacture of zeolites (Li et al. Reference Li, Jiang, Liu, Shi, Zhang and Sun2017). The PAL 5A zeolite is also able to adsorb heavy paraffins, n-decane and n-pentadecane. The objective of the present study was to improve the adsorption performance of PAL 5A zeolites by adding the crystallization directing agent (CDA). The CDA can control the crystal size of the PAL 5A. The light paraffin, n-hexane, is used widely to produce high-quality solvent oils; it is generated on a large scale through a catalytic isomerization reaction that results in a product stream which consists of 10 to 30% n-hexane. The PAL 5A zeolite products were characterized by powder X-ray diffraction (PXRD), scanning electron microscopy (SEM), and nitrogen adsorption. The batch adsorption performance was investigated with n-hexane (nHEX), 2-methylpentane (2MP), and 3-methylpentane (3MP) as the adsorbates. Fixed-bed adsorption breakthrough experiments were carried out to measure the amount adsorbed of binary mixtures of nHEX/2MP and nHEX/3MP.
EXPERIMENTAL
Materials and Reagents
The raw material for the synthesis of 5A zeolites used in this study was commercial PAL supplied by Xuyi Clay R&D Center of Changzhou University in China; the average particle size of the PAL was 75 μm. The chemical composition of the PAL, analyzed by X-ray fluorescence is: SiO2 (58.78%), Al2O3 (5.12%), Na2O (0.10%), K2O (1.29%), CaO (7.26%), MnO (0.05%), TiO2 (1.49%), Fe2O3 (4.79%), and MgO (10.09%) (Chen et al. Reference Chen, Wang, He, Chen and Zhang2016).
Sodium silicate, sodium hydroxide (≥98%), anhydrous calcium chloride (≥96%), sodium aluminate (≥98%), isooctane (≥98%), nHEX (≥98%), 2MP (≥98%), and 3MP (≥98%) were purchased from Aladdin Reagent Co. (Shanghai, China) and used without any pre-treatment.
Synthesis of Crystallization Directing Agent
The amorphous CDA, also known as a 'seeding director', plays a role in directing crystallization and crystal-size reduction in the synthesis of zeolite A. The synthesis steps are as follows: the aluminate solution was prepared by dissolving 1.31 g of sodium aluminate and 7.18 g of sodium hydroxide in 25 mL of deionized water under magnetic stirring; the silicate solution was prepared by mixing 2.44 g of sodium silicate and 20 of mL deionized water; then the silicate solution was poured quickly into the aluminate solution with vigorous stirring for 24 h, to produce a milky white sol-gel, with the theoretical molar composition of 12Na2O:SiO2:4.5Al2O3:350H2O.
Synthesis of 4A Zeolite (Na-A Zeolite) from PAL
Before preparing the 4A zeolites, the PAL was calcinated at 800°C for 4 h in a muffle furnace, then placed in 1 M HCl solution and stirred for 2 h to remove impurities, washed thoroughly until a pH = 7 was reached. In order to obtain the desired zeolites, a hydrothermal reaction was used. Sodium hydroxide was dissolved in 80 mL of distilled water, then 2.0 g of prepared PAL, 1.0 g of sodium aluminate, and CDA were added gradually to the sodium hydroxide solution. The mixture was stirred vigorously at 70°C for 4 h using a magnetic stirrer, forming aluminosilicate gel. The gel was transferred to a PTFE high-pressure reaction kettle (200 mL) and heated for 4 h at 90°C. The precipitates were separated from the liquid phase by filtration, washed with water until a pH value of < 9 was achieved, and then the materials produced were dried at 100°C.
Synthesis of 5A Zeolite (Ca-A Zeolite) through Ion Exchange
5A zeolite was synthesized by means of calcium ion exchange with the Na-A zeolite using a 1 M calcium chloride solution. With the 4A zeolite/calcium chloride solution ratio of 1:20 (mass/volume), the mixture was stirred in an ion exchange vessel at 95°C for 4 h. The 5A zeolite was separated by filtration and washed with distilled water. Then the product was dried at 100°C and calcined at 550°C for 4 h. This ion-exchange process was repeated once more in order to improve the extent of ion exchange. According to the mass ratio of CDA/deionized water added, three different types of 5A zeolites were obtained: CDA-5%, CDA-7.5%, and CDA-10%.
Characterization
X-ray powder diffraction (XRD) patterns were collected at room temperature using a Rigaku D/MAX-2500PC diffractometer (Rigaku Co., Tokyo, Akishima, Japan) using CuKα1 radiation (λ = 0.15406 nm) operated at 40 kV and 100 mA. Field-emission scanning electron microscopy (SEM) images of 5A zeolite products were taken at 30 kV using a Supra 55 microscope (ZEISS, Jena, Thuringia, Germany). N2 adsorption isotherms were measured at 77 K using an ASAP2020 sorption analyzer (Micromeritics, Norcross, Georgia, USA). Prior to each analysis, the samples were outgassed at 150°C for 4 h. The Brunauer-Emmett-Teller (BET) method was utilized to calculate the specific surface areas (S BET) using adsorption data in a relative pressure range from 0.05 to 0.30. The pore-size distributions and pore volume were derived from the adsorption branches of the isotherms.
Batch Adsorption Experiments
Vapor-phase batch adsorption measurements were performed on an Intelligent Gravimetric Analyzer (Model IGA-100B, Hiden Isochema Instrument, Warrington, Cheshire, UK) with a high sensitivity of 0.1 μg. The instrument has an ultrahigh vacuum system controlled precisely by a computer allowing accurate gravimetric changes to be recorded at gradually increased relative pressure values. The variations with time of the amounts adsorbed were also recorded. Before all measurements, pretreatment of each sample was conducted by degassing overnight at 120°C in a vacuum to remove the physically adsorbed water molecules and other impurities adsorbed in the pores. The batch adsorption experiments were carried out at 25°C.
Dynamic Adsorption Breakthrough Experiments
The dynamic adsorption separation was investigated using breakthrough experiments of binary mixtures of n-hexane/2-methylpentane (nHEX/2MP) or n-hexane/3-methylpentane (nHEX/3MP). To test reproducibility, parallel dynamic experiments were carried out three times. The breakthrough experimental apparatus comprised a feed pump, a stainless steel adsorption column, and a regulating valve at the outlet of a packed bed in order to collect products. The pump used to inject the mixture was a high-pressure, constant-current pump. The stainless steel column (10 cm long, 1.0 cm inner diameter) containing adsorbent (1–2 g) and quartz sand at the bottom was placed in an oven which maintained the temperature of the adsorption experiment at 200°C. The experiments were operated by continuously introducing mixtures of hexane isomers with known composition at a fixed total pressure and adjusted to keep a total flow rate of 0.5 mL·min–1. When saturation was reached, the composition of each product was analyzed using a Shimadzu GC2010 chromatograph equipped with a flame ionization detector (FID). The mass fractions of inlet mixtures were nHEX:2MP (or 3MP) = 1:1, 1:2, or 1:3, with isooctane (70%) as the solvent. The fixed total pressure was 0.5 MPa, 0.8 MPa, or 1.2 MPa, respectively.
The equilibrium dynamic adsorption capacity (q c) of the adsorbents was calculated from the breakthrough curves according to the equation as follows:

where C i and C 0 are the outlet and inlet mass concentrations (%) of the stream through the fixed bed column, respectively; u (mL·min–1) is the volume flow rate of the specific hexane isomers; m (g) is the dosage of the adsorbent; V' (mL) is the dead space volume of adsorbent bed voids and around the pipe; and ρ (g·mL–1) is the density of the binary mixture.
The feed flow rate u of the liquid phase was 0.5 mL·min–1, controlled by a high-pressure constant-current pump, and the exit flow rate was variable because one component was being adsorbed selectively. The mass of component i retained in the adsorbent bed was equal to the total inlet mass of i minus the total outlet mass of i, also minus the dead space volume of the bed.
is the total outlet mass of component i by integration of the breakthrough curves measured in terms of outlet concentration as a function of time.
The separation factor, S, for a binary mixture of components i and j, is defined as:

where q i and q j are the dynamic adsorption capacity of components i and j, respectively; c 0i and c 0j are the mass concentrations of the feed.
RESULTS AND DISCUSSION
Synthesis and Characterization
Powder XRD patterns of three as-synthesized 5A zeolite adsorbents based on PAL with various additions of CDA (Fig. 1) showed the characteristic peaks of 5A zeolite at 2θ values by comparing the PXRD patterns with standard simulation patterns from the literature (Treacy & Higgins Reference Treacy and Higgins2001). SEM images (Fig. 2) revealed that the particles of 5A zeolite were submicron crystals with cubic lattice shapes. All crystals of 5A products had an average particle size of 400–800 nm, which is smaller than that reported in the literature; most reports of the particle size of 5A zeolite are >1 μm (Li et al. Reference Li, Kuppler and Zhou2009; Yuan et al. Reference Yuan, Chen, Chang and Li2011). The amounts of CDA evidently control the morphology of 5A zeolites. With an increase in the amount of CDA, the change in the crystal size is not obvious, but the crystal shape of product CDA-10% has irregular cubic edges because of the introduction of an excessive amount of CDA. The system lacked sufficient crystals for nucleation and growth, which resulted in an incomplete reaction (or crystal growth) (Liang et al. Reference Liang, Zhang and Liu2001; Pu et al. Reference Pu, Zhao, Guo and Lv2004).

Fig. 1 PXRD patterns of three 5A zeolites with various additions of CDA.

Fig. 2 SEM images of three 5A zeolites with various additions of CDA
Nitrogen adsorption/desorption isotherms gave the specific surface area and the pore diameters (Table 1). In these products, PAL 5A (CDA-5%) showed the largest BET surface area of 527 m2/g and the micropore volume of 0.42 cm3/g. These values are larger than those for the PAL 5A zeolite (CDA-0%), which had a BET surface area of 482 m2/g and total pore volume of 0.27 cm3/g (Chen et al. Reference Chen, Wang, He, Chen and Zhang2016). The isotherms (Fig. 3) of all PAL 5A zeolite products showed type I Langmuir isotherms at low relative pressures, with a characteristic microporous adsorption. When the relative pressures were >0.8, the uptake increased and a smaller hysteresis loop was visible; this may be due to the properties of unreacted PAL.
Table 1 Pore-structure parameters

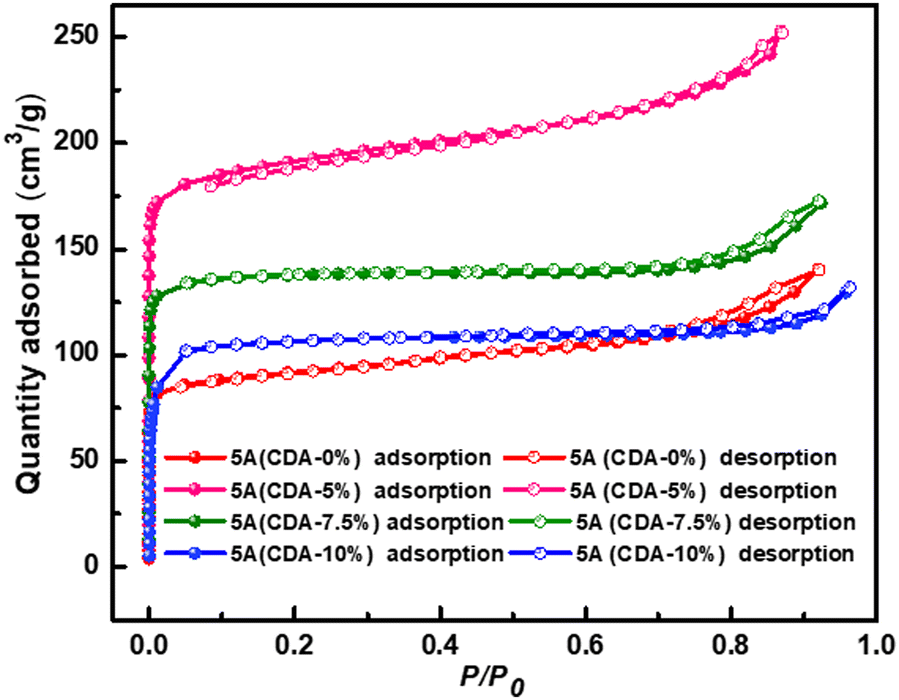
Fig. 3 N2 adsorpton/desorption isotherms of four 5A zeolites with various additions of CDA.
Batch Adsorption Performances
A batch adsorption test using the IGA-100B instrument was conducted to investigate the adsorptive properties and rates of interaction of the 5A materials with nHEX. Batch adsorption curves of pure nHEX, 2MP, and 3MP on PAL 5A materials (Fig. 4) revealed that the quantities of nHEX adsorbed on three PAL 5A zeolites were greater than those of 2MP and 3MP. The PAL 5A (CDA-5%) showed a faster rate of adsorption of nHEX than those of 5A (CDA-7.5%) and 5A (CDA-10%) (Fig. 4a). After 20 min, the adsorption capacity of nHEX on PAL 5A (CDA-5%) reached 80% of the saturation value, while the other two 5A zeolite products only reached 60% and 25%, respectively. Thus, the specific surface area and pore volume of PAL 5A (CDA-5%) are larger than those of PAL 5A (CDA-7.5%) and 5A (CDA-10%) (Table 1), so the adsorption of n-paraffin is expected to complete more easily. Due to the smallest surface area and the pore size of PAL 5A (CDA-10%), the resistance to diffusion of alkane molecules will be greater and entry to the pores will be more difficult, resulting in less adsorption. The optimal mass ratio of CDA/deionized water was ~5%, therefore.

Fig. 4 Batch adsorption rate curves of a nHEX, b 2MP, and c 3MP on PAL 5A zeolites
The sieving radius of 5A zeolite was reported to be close to 0.50 nm (Breck Reference Breck1974), which could be the reason for its efficiency in sieving branched hexane isomers with nHEX being adsorbed. The kinetic diameter of 2MP and 3MP molecules are both 0.50 nm, while nHEX’s kinetic diameter is 0.43 nm. The static kinetic measurements demonstrated that kinetic separation of paraffins is based on the molecular dimensions of the hexane isomers; and small amounts of 2MP or 3MP isomer may be adsorbed under larger diffusional limitations, so the adsorption rate of nHEX is greatest among the hexane isomers.
The one-component isotherms of nHEX, 2MP, and 3MP vapor adsorbed on four PAL 5A zeolites were measured at 25°C (Fig. 5). The static saturation adsorption capacities of nHEX adsorbed on PAL 5A (CDA-0%), 5A (CDA-5%), 5A (CDA-7.5%), and 5A (CDA-10%) were 0.136 g/g, 0.149 g/g, 0.120 g/g, and 0.0780 g/g, respectively (Fig. 5a). The PAL 5A (CDA-5%) was superior to many previously reported commercial 5A zeolite adsorbents synthesized from natural clays, which have the adsorption capacity of nHEX at ~0.08–0.13 g/g (Sun et al. Reference Sun, Shen and Liu2008; Melo et al. Reference Melo, Riella, Kuhnen, Angioletto, Melo, Bernardin, da Rocha and da Silva2012). Meanwhile, 5A (CDA-5%) zeolites synthesized in the present study have greater adsorption capacity for nHEX than commercial Sinopec 5A synthesized from chemical raw materials with the amount of nHEX adsorbed of 0.117 g/g (Sun et al. Reference Sun, Liu, Huang and Shen2006).

Fig. 5 Batch adsorption isotherms of a nHEX, b 2MP, and c 3MP on PAL 5A zeolites.
The saturation adsorption capacities of nHEX on four PAL 5A zeolites were greater than those of 2MP and 3MP. By comparison with the structural features of hexane isomers, the lower adsorption capacity of 2MP and 3MP on 5A can be attributed to their larger kinetic diameters. On the other hand, the static saturation adsorption capacity of 3MP adsorbed on four PAL 5A zeolites was slightly greater than that of 2MP (Fig. 5b and c). For all three adsorbents, product PAL 5A (CDA-5%) exhibited the largest adsorption capacity for nHEX and smallest adsorption capacity for 2MP and 3MP, while product PAL 5A (CDA-10%) displayed the smallest amount of adsorption for nHEX. Product PAL 5A (CDA-5%) displayed better adsorption equilibrium selectivity than those of product PAL 5A (CDA-7.5%) and PAL 5A (CDA-10%) for nHEX/2MP separation. The amount of adsorption increases with increase in pressure (Fig. 5).
Dynamic Adsorption Breakthrough Experiments of Binary Mixture Composition
The PAL 5A (CDA-5%) was investigated further for its dynamic adsorption behavior with hexane isomers. This product was chosen due to its distinct static adsorption performance among the 5A zeolite adsorbents investigated. Two sets of experiments were carried out: (1) the influence of the initial feed concentration at a fixed total pressure and temperature for hexane isomers; and (2) the influence of the total pressure at a fixed feed concentration and temperature for hexane isomers. In accordance with industrial separation conditions (Lu et al. Reference Lu, Du, Yao, Liu, Cui, Wang and Yao2010), the dynamic experiments were performed at 200°C and up to 1.2 MPa in the fixed-bed adsorption experiment column.
Breakthrough curves of nHEX/2MP, nHEX/3MP mixtures on 5A (CDA-5%) with different feed ratios at 200°C and 1.2 MPa were obtained (Fig. 6). After the injection of a mixture of nHEX and 2MP (or 3MP) at the inlet of a column packed with 5A zeolite, the linear chain eluted later than its branched isomer, indicating preferential adsorption of nHEX. The outlet concentration of 2MP (or 3MP) increased rapidly to the feed concentration level within 20 min. When the feed ratios of nHEX/2MP and nHEX/3MP mixtures were 1:2, the longest adsorption equilibrium time occurred after ~30 min (Fig. 6). The dynamic saturated adsorption capacities of nHEX increased with the adsorption equilibrium time being extended. The shape of the breakthrough curves depended mostly on mass transfer kinetics, indicating the impact of feed concentration. The experimental conditions and results are given in Tables 2 and 3.

Fig. 6 Breakthrough curves of nHEX/2MP and nHEX/3MP mixtures on PAL 5A (CDA-5 %) with various feed ratios.
Table 2 Experimental conditions and dynamic adsorption parameters for nHEX/2MP binary breakthrough curves on 5A (CDA-5%).

Table 3 Experimental conditions and dynamic adsorption parameters for nHEX/3MP binary breakthrough curves on 5A (CDA-5%).

The breakthrough curves of binary mixtures (nHEX:2MP = 1:2 and nHEX:3MP = 1:2) at various total pressures on PAL 5A (CDA-5%) were obtained (Fig. 7). Breakthrough curves of nHEX on 5A zeolite indicated that its adsorption is highly favorable at higher total pressure. The dynamic adsorption capacity of nHEX increased with increase in total pressure; the outlet concentration of nHEX adsorbed increased slowly after 5 min, until dynamic equilibrium was reached after 30 min (Fig. 7). The conditions for the largest nHEX/2MP separation selectivity were achieved with a feed concentration ratio of 1:2 at a total pressure of 1.2 MPa (Table 2), while the conditions of the largest separation selectivity of nHEX/3MP were at a feed concentration ratio of 1:3 and a total pressure of 1.2 MPa (Table 3). 5A zeolite synthesized from PAL exhibited significantly better shape selectivity and adsorption capacity toward nHEX than toward 2MP and 3MP under the aforementioned experimental conditions. As a low-cost, natural starting Si/Al source, PAL was proven here to be a potential substitute raw material for the synthesis of 5A zeolite adsorbent.
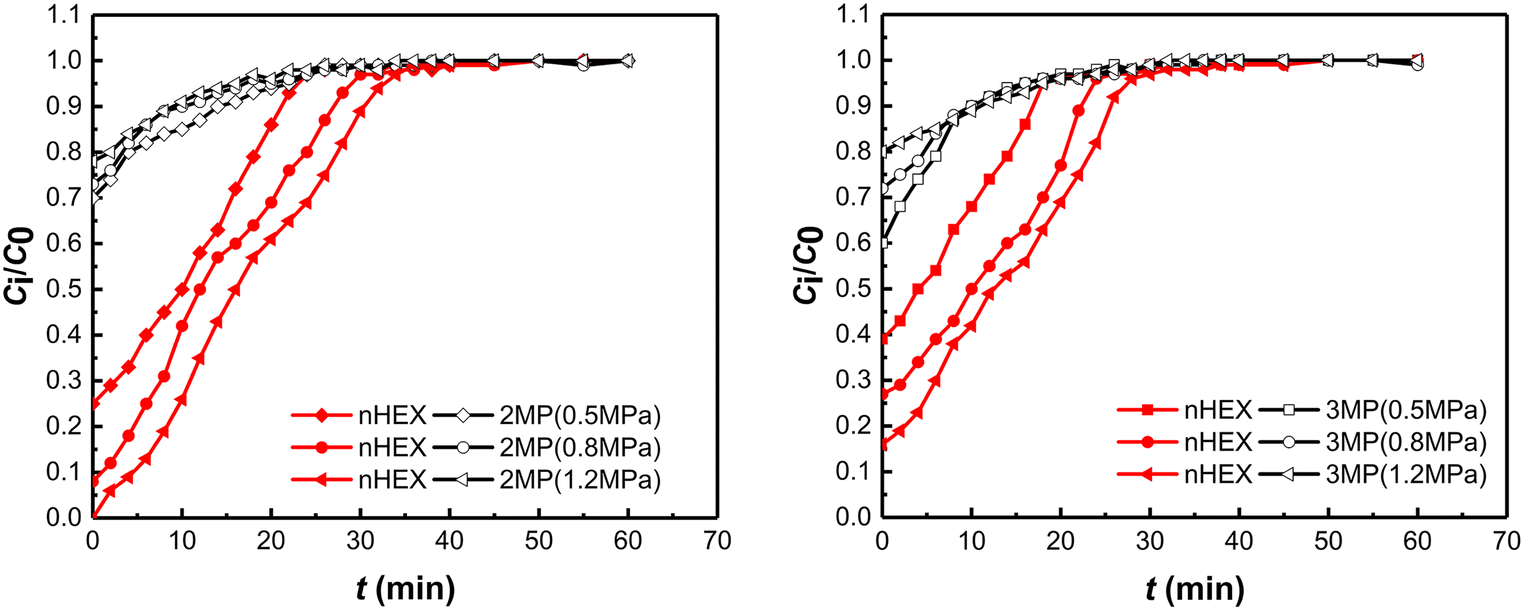
Fig. 7 Breakthrough curves of nHEX/2MP and nHEX/3MP mixtures at various total pressures on PAL 5A (CDA-5%) (nHEX:2MP = 1:2 and nHEX:3MP = 1:2).
Conclusions
Submicron 5A zeolites have been synthesized successfully from the natural clay mineral PAL with the addition of pre-synthesized CDA. The amount of CDA added was found to control the crystal size of the 5A zeolite crystals in the range of 400–800 nm. The most suitable mass ratio of CDA/deionized water was ~5% according to the batch adsorption performance. The maximum adsorption capacity of nHEX was 0.149 g/g for all PAL 5A zeolites, which is superior to those of 2MP or 3MP. Dynamic adsorption investigation showed that the conditions for the largest nHEX/2MP separation selectivity were achieved with a feed concentration ratio of 1:2 at a total pressure of 1.2 MPa, while the largest selectivity of nHEX/3MP was achieved with the feed concentration ratio of 1:3 at a total pressure of 1.2 MPa. In contrast, with chemical Si/Al sources, PAL was proven to be a low-cost and environmentally friendly Si/Al source and a potential substitute raw material for the synthesis of 5A zeolite on a large scale.
Electronic supplementary material
The online version of this article (https://doi.org/10.1007/s42860-019-00057-6) contains supplementary material, which is available to authorized users.
ACKNOWLEDGMENTS
The authors gratefully acknowledge financial support from the National Natural Science Foundation of China (Grant 11775037), the Natural Science Fund for Colleges and Universities in Jiangsu Province (grant 16KJD530001), and Jiangsu Key Laboratory of Advanced Catalytic Materials and Technology (BM2012110). The Graduate Students Cultivation and Innovation Project of Jiangsu Province (KYCX17_2081) is also acknowledged.
Notes
The authors declare no competing financial interest; all authors are members of Changzhou University.